Best Manufacturing Inventory Software
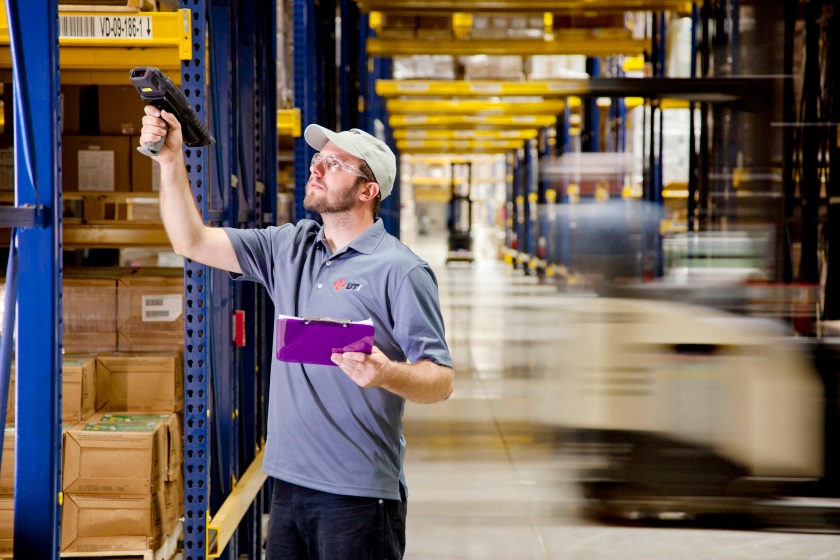
You can also listen to this article:
What is inventory? The answer is obvious. Inventory is everything that is in the warehouse – in pieces, or in money.
It is a list of stock items with their quantities and sums, grouped by an item, by shelf, by lot/batch and including (or excluding) items that are usually procured/sold by the company. Inventory is just one number: the total cost of goods that are currently in stock.
So, the word ‘inventory’ can have many meanings. They all are connected with each other, but still serve different purposes.
Similarly, there are many software packages that have inventory management functionality. But they focus on different aspects of inventory management. Some are good at handling a list of items with beautiful images, attractive marketing texts in different languages, etc. Others are good for accounting purposes. They show total assets immediately. Others are good at managing inventory levels.
What is important for a manufacturing company, and how to choose the best manufacturing inventory software
One of the most important functions of the software is that it must understand that in manufacturing, as opposed to wholesale or logistics, some items (materials) come into the stock, and other items (final products) go out of stock. Theoretically, it is possible to manually write off materials as if they were lost and add final products as if they were found, appearing from nowhere. But this ruins reporting.
Though material consummation functionality seems to be obvious, from a technical point of view, it is not so easy; there are good and well-known accounting packages that contain inventory management, but openly declare that their inventory management is not suitable for companies that manufacture goods for sale.
The second important functionality is the ability to track lots/batches separately. Many inventory management software packages store inventory as a list of products with their quantities as one number per item. They do not store each lot separately. When an item is purchased, the number increases; when an item is sold, the number decreases. An ‘average cost method’ was invented by accountants to calculate the approximate cost. This type of inventory is easier to handle (especially if done manually) and it is suitable for many businesses unless they need to:
- Use FIFO
- Be able to trace from which materials some particular product was made
- Track expiry dates
One more function, which is often overlooked, but can save a lot of time, is the ability to adjust inventory levels of many items at once. In wholesale, what was procured gets sold or returned to the vendor. The quantities match. If some quantity does not match, then the reason should be investigated. In manufacturing, there are materials and final products, but also consumables.
Materials are used according to a plan and products are sold according to customer orders. But quantities of consumables can vary. And when a stocktaking is made, it may be needed to update quantities of many items. Doing this one by one is inefficient. Having a page with a list of all items and the ability to update many quantities at a time saves a lot of effort. But if the software is focused on strict control, then it may not have such functionality.
To sum up, manufacturing companies have special requirements regarding inventory management, which sometimes are in contradiction to other industry requirements. Because of that, not every inventory management software, which may be quite advanced, is suitable.
More information about manufacturing inventory software: