Batch Tracking – A Simple Guide
Batch tracking is a functionality that no batch production setup should go without. In this guide, we look at the fundamentals of batch tracking and see how MRP software can help achieve traceability.
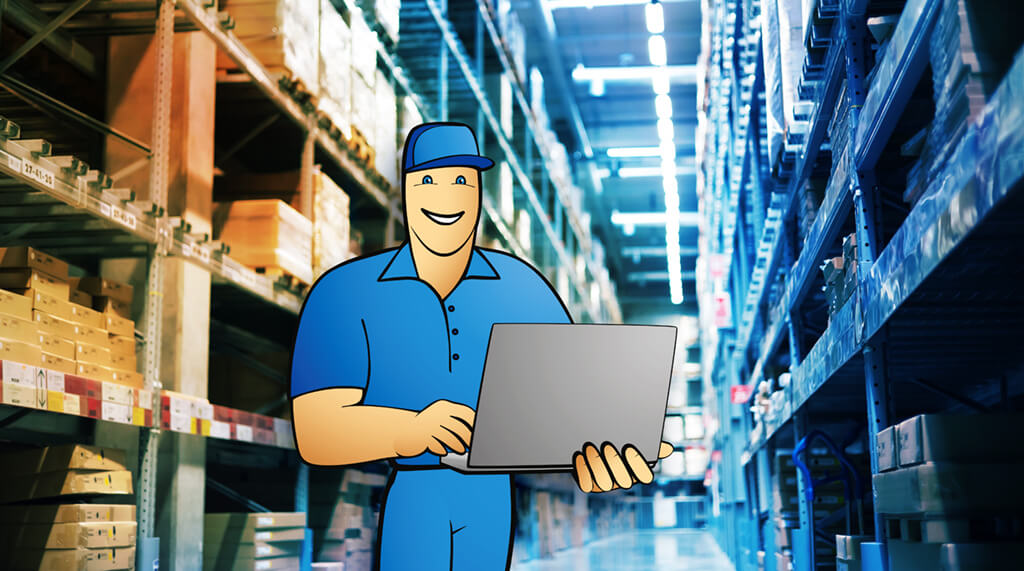
You can also listen to this article:
What is batch tracking?
Batch tracking is the ability of a production or inventory management system (IMS) to monitor and keep track of batches of products throughout their manufacturing journey and the supply chain. A batch is a group of identical products or components that are manufactured together or that exit a single manufacturing process together in the case of subassemblies.
As the name implies, batch tracking is only applicable to batch production workflows wherein multiple identical items or “batches” of goods are manufactured at once. Batch production is mostly common for process manufacturers, however, discrete manufacturers often also have parts of their workflows set up in a batch process.
Batch traceability is achieved by assigning batch numbers to manufactured goods and using either traceability software or manual methods to track the various data contained in them. For example, capable IMS or production management systems with batch tracking functionality generate and assign batch numbers automatically. These can then be printed out as labels or barcodes and taped to finished products or racks, or assigned to physical items using machine vision systems.
Batch numbers can be customized to include a wealth of information about the product batch such as its manufacturing date, expiration date, involved workstations, routing information, raw material sources, etc. In the modern manufacturing landscape, traceability is exceedingly important for assuring regulatory compliance, handling recalls and RMAs, simplifying quality control, optimizing inventories, and raising the overall level of control over the manufacturing system and supply chain.
Batch numbers vs lot numbers
While the two terms are often used interchangeably, batch numbers are technically distinct from lot numbers. As we explained, a batch is a group of identical products that are manufactured together. All products in a batch share a batch number. A lot, on the other hand, is an inventory term that designates a particular quantity – a “lot” of materials that is stored or procured at the same time and from the same supplier.
A stock lot always consists of identical items with the same batch number. However, a large number of goods with the same batch number might have different lot numbers in the IMS. For example, if they are sold off in smaller quantities or when a supplier sends multiple smaller lots of goods over time to a manufacturer that all originate from one large batch.
The chief difference between lot and batch tracking is quite straightforward. Lot tracking enables tracking what lot(s) a batch of goods has been sent to or stored at, while batch tracking enables tracing back a particular product to the manufacturing process e.g. the specific workstation and sales order that it originates from.
It’s worth noting that in inventory software, batch tracking is mostly realized through lot tracking.
Read more about lot tracking in manufacturing.
What is the difference between batch numbers, SKU codes, and serial numbers?
Let’s also clear up the difference between batch numbers and other common inventory identifiers – SKU codes and serial numbers.
An SKU code is a unique identification number that is assigned to every component or product of the same kind in an inventory system. For example, if a cupcakes manufacturer produces many flavors of cupcakes, each flavor of cupcake will have a different SKU code and every cupcake of that flavor shares the same SKU code.
While a single batch of products all have the same SKU code and batch number, the next batch of the same product has the same SKU code but a new batch number. If a particular batch of goods is stored in two different locations, however, both of these may also have different lot numbers, while sharing the same batch number.
Serial numbers, on the other hand, differ from both SKU codes and batch numbers in that they are assigned to every individual product or component separately. Serial number tracking is usually not used in batch production workflows, especially in process manufacturing. However, if per-item traceability is required, tracking both serial and batch numbers in concert is possible.
The importance of batch traceability
Any modern manufacturing or distribution operation has a lot to gain from end-to-end traceability, whether it’s achieved through batch, lot, serial number tracking, or a combination of these. Next, let’s look at the prime benefits that batch traceability can bring.
Regulatory compliance
Many industries and markets require businesses to maintain records of their manufacturing processes and distribution. Prominent examples include pharmaceuticals, food and beverage, automotive, and electronics. Having a robust batch tracking system simplifies meeting these requirements, smoothing the audit process, reducing the risk of non-compliance penalties, and above all, helping to ensure that the products conform to quality and safety standards. Batch traceability also helps to demonstrate the transparency of operations and instill confidence in regulatory bodies.
Expiration date tracking
Next to compliance, one of the key benefits of utilizing batch numbers lies in the ability to track the expiry date of perishable goods. Expiry date tracking prevents the accidental sale or use of expired products and hugely simplifies managing product rotations. This is particularly crucial for food safety and in pharmaceuticals production where the consumption of products past their shelf life could lead to health hazards. Expiration tracking can also be useful financially, however, for preventing losses associated with spoilage or even managing timed promotions.
Accurate inventory sequencing
In terms of inventory management and sequencing, batch tracking helps facilitate inventory valuation methods like FIFO (First-In, First-Out), LIFO (Last-In, First-Out), and FEFO (First-Expired, First-Out). These are crucial for reducing obsolescence and waste as stock can be sorted and sequenced by their production or expiry dates – information easily accessible via the stock’s batch information. FIFO ensures that the oldest stock is used or sold first, LIFO achieves the opposite, and FEFO prioritizes utilizing items closer to their expiration date. The above methods also influence a company’s bottom line and taxation requirements in different ways, providing more control over a company’s financials.
Quality control and Q/A
Batch traceability is a cornerstone of effective quality control and quality assurance. It allows manufacturers to monitor the quality of their raw materials and products throughout the production process. By tracking batches, any quality issue can be quickly isolated to a specific batch, limiting the required scope of quality inspections and making problem-solving faster and more cost-effective. This simplifies maintaining high standards of product quality and also helps to enhance brand reputation.
Easier callbacks and RMAs
In the event of a product recall or RMA (return merchandise authorization), batch traceability significantly simplifies the recall process. If an issue arises with an item, a business can use the batch number to investigate the source of the problem and pull the entire batch off the market if necessary. This way, a single refund or exchange case can be grounds for designating a whole batch for quality control. This targeted approach represents an added layer of control and minimizes the financial and reputational impact of quality issues. What’s more, batch tracking helps customer support to provide a more efficient service by having more information on the product and how to take appropriate action.
Batch tracking with traceability software
Maintaining batch traceability manually can be a daunting task, especially for businesses with complex distribution chains and large inventories. Manual tracking involves managing extensive records in spreadsheets that are known to be prone to errors and oversights. Manual methods also lack the speed and real-time data access necessary for efficient decision-making, particularly when a company starts growing in production volume.
In contrast, using inventory management software or an MRP system with built-in batch tracking features has significant, and cost-effective benefits. This type of software automates large parts of the tracking process. It ensures accurate and efficient data management while simplifying regulatory compliance and quality control. Besides that, it also offers real-time visibility into inventory levels and movements.
MRPeasy’s batch tracking solution
MRPeasy’s batch and lot tracking functionality exemplifies the efficiencies that can be achieved with an advanced MRP system. MRPeasy automatically generates unique lot numbers for each purchased material and for each production run. During production planning, MRPeasy proposes which lot to pick materials from, following either the FIFO or FEFO principle, and helps to manage bookings to prevent overbooking. Workers are provided with detailed instructions on which materials to pick, including lot numbers, quantities, and locations.
For each sale, MRPeasy records the specific stock lots from which products are booked, enabling end-to-end traceability. Any defective products can be swiftly traced back to specific production operations or material purchases, making problem resolution efficient and targeted. The system also records the actual cost of each lot, facilitating accurate inventory management and cost analysis.
If a product is designated for quality control, the corresponding stock lot will be quarantined until it has been inspected. For items that fail quality control or are returned by the customer, service or repair orders can be scheduled within the software. MRPeasy also includes additional features such as the tracking of individual serial numbers within stock lots and the ability to attach notes and files, such as certificates, to individual stock lots.
Overall, MRPeasy’s batch tracking functionality offers a comprehensive solution for managing batch traceability. It eliminates many of the challenges associated with manual methods and enables the business to focus more on core operations and less on administrative tasks.
Key takeaways
- Batch tracking refers to the ability to track and monitor relevant information on goods produced in batches throughout the supply chain. Batch tracking is only applicable to batch production workflows.
- Batch tracking is achieved by assigning each batch of finished goods unique batch numbers. This enables end-to-end traceability – leaving a trail of production and logistics data on suppliers, materials and workstations used, etc., as the product moves through the supply chain to the end customer.
- Traceability is exceedingly important for assuring regulatory compliance, handling recalls and RMAs of defective items, simplifying quality control, optimizing inventories, and raising the overall level of control over the manufacturing system and supply chain.
- Batch tracking is technically possible using manual methods. However, dedicated production tracking software or a traceability functionality built into a competent inventory management system provides a far more cost-efficient solution by automating large parts of the tracking process and eliminating human errors associated with managing large datasets using spreadsheets.
Frequently asked questions
Batch traceability is the ability of a production or inventory management system (IMS) to monitor and keep track of batches of products throughout their manufacturing journey and the supply chain.
Batch traceability helps ensure that manufacturing and supply chain data is easily available for a product in all stages of its life cycle. Traceability is a regulatory requirement for many industries and simplifies handling product recalls, assuring quality, and optimizing inventory and production management.
Batch numbers can be tracked with manual or software-based inventory management systems. Manual tracking can be achieved to an extent using spreadsheets or other methods. However, the built-in traceability functionality of capable MRP/ERP systems or dedicated batch tracking software streamlines large parts of the tracking process, offering many advantages to manual workflows.
You might also like Manufacturing Supply Chain Management – Best Practices for SMEs