Batch Production – Benefits, Examples, and Tips
Batch production is a manufacturing process in which a group or “batch” of identical products go through production steps together. This reduces cycle times per product and enables goods to be manufactured flexibly in large quantities.
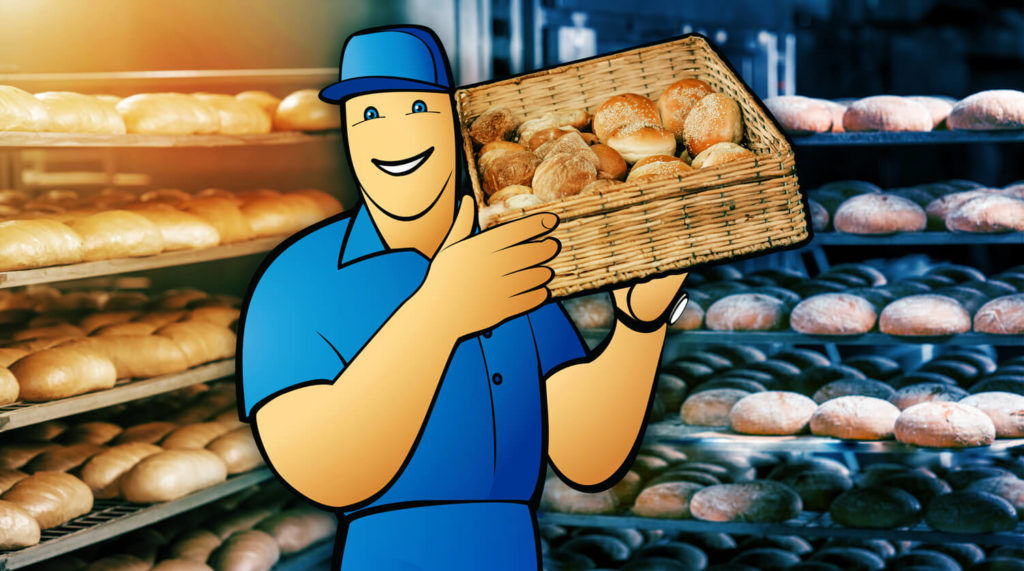
You can also listen to this article:
What is Batch Production?
Batch production is a manufacturing method where sets of identical goods go through production stages together, i.e. the production process creates a batch of finished goods at a time. In batch production, individual items do not pass to the next value-added phase until all of the products in the lot have made it through the previous step.
A batch process can consist of many different operations, where each one is configured to return a batch of items. To maximize production efficiency, it makes sense to align the number of items per batch between different steps. For this reason, it is common for batch manufacturers to utilize a lot of machine equipment, with workers being involved mostly at the beginning and end of the process and for quality control.
Batch production is most commonly associated with process manufacturing operations in which goods are produced by mixing or blending components together in a process, such as food, chemicals, pharmaceuticals, etc. Nevertheless, it can also be used in discrete manufacturing, where products are assembled from separate components and can later be disassembled, like electronics or industrial equipment.
Read more about Process Manufacturing vs. Discrete Manufacturing.
Batch Production vs. Mass Production vs. Job Shop Manufacturing
As a manufacturing term, batch production belongs to a group of manufacturing processes that are differentiated by their scale. The other two in the group are mass production (products made in very large quantities, usually in a continuous flow) and job shop manufacturing (products made in single copies or in small series, often as custom orders).
Apart from the scale of production, aspects that vary between those three types of manufacturing processes are:
- Mix of products. Job shops can produce an array of different items customized to the specifications provided by the customer. Mass production creates a very limited mix of products. Batch production has a fairly limited range of products.
- Tools used. Job shops use general-purpose equipment, devices, and tools while mass production uses highly specialized ones. Batch production can use both general and special-purpose tools.
- Production floor organization. In job shops, workplaces are grouped so that similar tasks are performed in the same area; in mass production, the production line is built according to the course of the production process. In batch production, it is usually a mix of these approaches.
- Employee qualifications. Job shop employees are usually highly qualified and able to perform a diverse range of operations within their area of expertise. Mass production employees generally have lower qualifications and perform one specific operation. Batch production employees typically have an average qualification that allows them to perform a number of different operations.
- Production process development. In job shops, the production process is rarely developed in high detail as opposed to mass production where companies try to optimize each manufacturing operation to reduce costs, often opting for a high degree of automation. This applies especially to continuous production, a mass production system where the production line works continuously with raw materials constantly fed into the system and finished products constantly put out. In batch production, the production process is usually also highly optimized.
- Production costs. Job shop manufacturing costs per unit are very high compared to the other two types. Mass production cost per unit is, in turn, very low – this type of manufacturing is mostly used to produce consumer goods. Batch production, again, lies between the two others.
Some companies may not use a strictly defined production process, instead opting for a mixed-mode production style with characteristics from different types of manufacturing processes.
Learn more about the Types of Manufacturing Processes.
Advantages of Batch Production
Flexibility. Batch production allows companies to produce different goods using the same machinery. It also allows for a certain degree of customization when a client requests a whole batch of the product with some minor changes in it. Batch production also allows companies to scale the size of their batches to respond to fluctuations in demand.
Product variants. Products can be made in different colors, sizes, and other customizable parameters in large quantities. This allows companies to cater to a wider customer base while retaining their throughput rate. Managing large quantities of variants manually can be a very resource-heavy endeavor, however, so many manufacturers look to implement an ERP/MRP system with an integrated product configurator software.
Greater quality control. As batch production takes place in a series of steps, it is easy to check the quality of the product between them and to make necessary changes. This is more difficult in mass production, especially in continuous manufacturing, and depends on the age of the equipment and the level of add-on monitors and sensors required from one stage to the next. Frequent inspections allow companies to detect errors early on and avoid spending time and effort on already faulty products.
Cheaper than building single products. Producing batches of the same product costs less than manufacturing single items thanks to bulk raw materials and labor being cheaper, the process being more efficient, and the general-purpose equipment often requiring less capital investment.
Shorter lead times. As batch production processes often have the advantage of scalability, you can produce small batches during periods of low demand and scale up when necessary without the larger volumes having a significant effect on lead times.
Disadvantages of Batch Production
High WIP inventory levels. If products are moved from one operation to another in batches, then with a batch of 100 units and a single unit being processed at a time, the other 99 units will be idle. Concurrently, a similar situation may occur at each workstation on the shop floor.
Also, when one step in the production process is finished, there may be not enough production capacity to move the goods to the next stage immediately. This means goods have to be transferred to WIP inventory mid-process, which increases storage space and inventory labor requirements.
Errors can be costly. An undetected quality error can ruin a whole batch and end up wasting a lot of materials and time, especially when producing more expensive goods.
Idle time. Batch production can incur a considerable amount of downtime, be it due to machinery changeovers, quality checks between steps, or due to transferring goods to and from WIP inventory.
When to use Batch Production?
Batch production is best used in businesses where:
- goods are produced by blending raw materials according to a formula or recipe before moving to the next production step;
- low volumes of a single product are produced at a time, e.g. baked goods, flat-pack furniture, and low-volume designer items;
- demand dictates some degree of repetitiveness, i.e. when there are frequent repeat orders for a single product;
- demand is seasonal, e.g. large batches of one product are made for sale in the summertime, then the machinery is changed over to produce another type of product for the next season.
Batch Production examples
Batch production can be used to manufacture a wide array of different goods, including but not limited to:
1. Baked goods. A bakery typically produces batches of many different goods, e.g. white bread, whole wheat bread, rolls, pastries, etc. using the same machinery.
2. Apparel. Clothes manufacturers typically batch-produce variants of the same product, e.g. a t-shirt can have variations in color and size.
3. Flat pack furniture. One of the most popular furniture brands in the world, Ikea, uses batch production to manufacture their self-assembly furniture.
4. Soaps and shampoos. With these types of items, a large batch of the product is made before dividing it into appropriate volumes for consumers.
5. Pharmaceuticals. Similarly with other chemicals, pharmaceutical products are made in batches, then divided and packaged for consumption by their end-users.
6. Electronic components. PCB boards as well as various electronic components are usually made in batches due to the nature of the manufacturing process. E.g. many computer processors are made on a single silicon wafer at a time.
7. Electronics. When making electronic devices, even if these are mass-produced and one-piece flow is used at later assembly stages, batch production may be used at certain production steps, e.g. when placing electronic components on PCB boards.
The importance of Batch Tracking
Lot tracking or batch tracking essentially means keeping records of the movements and events related to the manufacture of specific batches.
When a batch of goods is received from the supplier, it is given a stock lot number that helps identify this lot later in the process. Similarly, when this lot is used in the production of a batch of finished goods, the new batch is assigned another lot number. Simply put, lot tracking can help keep tabs on which raw materials were used in which products, which suppliers provided the materials, and which customers have purchased the finished products.
This record-keeping is crucial for achieving the end-to-end traceability required in today’s highly regulated markets. It allows companies to track supplier quality, trace back errors in the production process, keep tabs on expiry dates, organize product callbacks, etc.
While it is possible to do all this manually, it is a very time-consuming task. This is why most forward-looking companies choose to implement an ERP/MRP system with built-in traceability software functionality that automatically updates the data whenever a label is scanned, for example when parts of a stock lot are consumed on the production floor.
Batch production management with MRP software
MRP or manufacturing ERP software is quickly gaining ground among small and medium-sized companies within the sector. With benefits ranging from significantly more accurate production planning and production scheduling to optimized inventory, workflows, and supply chains, and efficient communication within the company as well as with suppliers and customers, MRP software is a logical step forward from spreadsheets.
But is manufacturing ERP/MRP software suitable for the batch production method? Undoubtedly.
Here are some of the benefits it brings to the batch manufacturing process specifically:
- Batch size optimization. MRP software can use historical data to give you a detailed analysis of the costs associated with specific batches, allowing you to find the optimal batch size in terms of cost efficiency. MRP software also shows you exactly how much you can produce at any given time considering your production capacity and inventory levels.
- Batch tracking. Stock lot tracking is an essential part of any respectable MRP software, allowing batch manufacturers to know exactly which lots were used in which finished batches, where the materials came from, and where the finished products went to.
- Effective quality control. With quality inspection and batch tracking functionalities, MRP software allows you to a) have an overview of the quality of both incoming raw materials as well as finished goods, and b) trace back any quality inconsistencies to specific material lots, suppliers, workstations, or employees.
- Scheduling flexibility. MRP software can be used to automatically schedule production according to available material quantities and production capacity Some software solutions also have manufacturing operations overlap functionality, which allows batch manufacturers to start the next operation in the process when the previous one has not completely finished. For example, when 10 out of 100 tables have finished, the next step, applying the finish, can start on the already completed 10 tables.
- Batch-specific reports. MRP software is made for collecting, processing, and displaying vital manufacturing data. For example, you can use MRPeasy to generate production reports per batch, inspection reports per batch, industry-compliant electronic batch records, etc.
In addition, setting up a batch production process within a modern MRP software is quick, simple, and affordable.
Key takeaways
- Batch production is a manufacturing method where sets of identical goods go through different production stages together, i.e. the production process creates one batch of finished goods at a time.
- Even though batch production of most commonly associated with process manufacturing, i.e. with the production of goods such as food, chemicals, pharmaceuticals, etc., it can also be used in discrete manufacturing.
- Batch production differs from job shop manufacturing and mass production by its mix of products, tools used, production floor organization, employee qualifications, production process development, and production costs.
- The advantages of batch production are: flexibility, the possibility to create product variants, greater quality control, and low costs.
- The disadvantages of batch production are: high WIP inventory levels, possible high cost of errors, and increased idle time.
- Batch production facilities should have a lot tracking system in place to ensure traceability and regulatory compliance.
- Apart from batch tracking, MRP software provides batch production companies with many other benefits that allow them to increase efficiency across the board.
Frequently asked questions
Batch production is a manufacturing process where a predetermined quantity of products is produced at a time before moving on to the next set of products.
Batch production involves producing a predetermined quantity of products at a time with frequent changeovers, while mass production focuses on the continuous production of large quantities with minimal changeovers.
Examples of batch production include baked goods, pharmaceuticals, cosmetics, chemicals, automotive parts, electronic devices, and garments.
You may also like: What Is Traceability in Manufacturing and How to Achieve It?