Barcode Inventory Control – Benefits and Tips
Whether you run a small business or a large warehouse, managing inventory is key to smooth operations. Barcoding simplifies this task and makes the inventory process faster, more accurate, and much easier to handle.
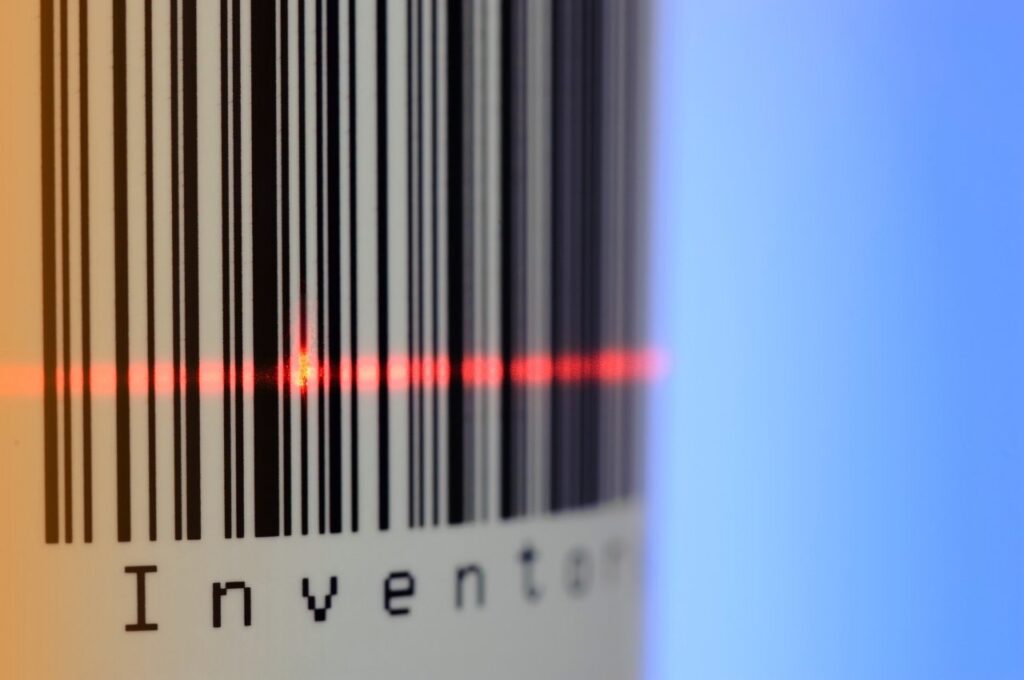
How can barcoding increase inventory control?
Inventory control is about managing your stock so you always have what you need without having too much or too little. Good inventory control keeps the right balance and helps you avoid running out of items or overstocking. This saves money and prevents delays in e-commerce or production.
Barcodes help streamline inventory management in several key ways:
- Track stock levels. Barcode scanning can update stock levels in real time to reduce human error in data entry.
- Receiving and shipping. Barcodes let you quickly scan incoming shipments and check them against your purchase orders. They also ensure accurate shipping because your team can scan items before they leave the warehouse.
- Product identification. Barcode systems simplify managing stock-keeping units (SKUs), as every SKU or individual item can be assigned a unique barcode.
- Physical counting. Barcodes speed up the stocktaking process, allowing for quick and accurate stock counts and cycle counts and simplifying the keeping of accurate inventory records.
- Inventory management efficiency. While barcodes themselves don’t trigger actions, scanning them at key points, such as when receiving shipments, can optimize stock control. This way, if the stock falls below a reorder point, your inventory management system (IMS) can prompt an alert to prevent stockouts.
But let’s take a step back and see what barcodes are in order to further understand their utility.
What are barcodes?
Barcodes are machine-readable images made up of lines or shapes that hold digital data. When scanned, they enable the identification and tracking of inventory items associated with them. They turn information into a machine-readable pattern, usually consisting of black lines and white spaces (for 1D barcodes) or shapes (for 2D barcodes like QR codes or data matrices). When scanned, this coded information gets decoded into something your inventory management system can understand, such as product IDs or serial numbers.
While both traditional and two-dimensional barcodes store data, they have key differences. When deciding which to choose, you should consider the amount of data you need to store and where and how they’ll be used. Here’s a closer look at each type and where they shine.
1D barcodes for quick, universal use
Traditional barcodes, made of vertical lines, are commonly seen on products and store simpler data, such as a universal product code (UPC) or a European Article Number (EAN). They require a barcode scanner to read and are perfect for inventory control due to their speed and simplicity in scanning. 1D barcodes are widely used for basic tasks like tracking inventory and pricing.
QR codes for more information
A type of two-dimensional barcode, QR codes consist of square grids that can hold more data than 1D codes, such as URLs, text, or other details. QR codes are easily scanned with a smartphone, which makes them ideal for consumer-facing uses such as marketing, payments, or website links. They are best for handling more complex information and can help with product traceability as they can store batch details or inspection data.
Data matrix codes for high-density, compact use
Data matrix codes are two-dimensional codes, much like QR codes, but excel in industrial and high-precision applications where space is limited. Due to their small, compact design and high data density, they work especially well in manufacturing and aerospace or healthcare, where tracking small, critical parts is essential. These codes are usually crafted to withstand harsh environments and maintain readability on tiny items like circuit boards, medical devices, or aerospace components.
The importance of inventory control
Effective stock control is essential for keeping your operations running smoothly. For manufacturers, it’s crucial to maintain this balance because mismanaged stock can lead to production delays, increased costs, or missed sales opportunities. Here are some tips for improving stock control and how barcoding can help:
- Set clear reorder points. Establish reorder points for each item in your inventory to prevent shortages and avoid costly delays in production. When an item is scanned as it’s consumed on the shop floor, you can stay informed on dwindling stock levels.
- Use real-time tracking. Tracking stock in real-time allows you to see exactly what’s available at any given moment. Barcodes make this easier by updating inventory levels instantly with each scan.
- Optimize storage and retrieval. Proper organization is key to finding and retrieving stock quickly. In a properly set up warehouse management system, barcodes can include data on an item’s exact location. This saves time and reduces picking errors.
- Implement regular cycle counts. Frequent cycle counts help you spot discrepancies early. Barcoding speeds up this process by allowing for quick, accurate scans without stopping operations.
What is a barcode inventory system?
A barcode inventory system is a tool that uses barcodes and scanners to track and manage inventory items. Stock items are assigned a barcode, which can be scanned in key points of the production pipeline to instantly update inventory levels, change order statuses, etc.
There are two main types of barcode inventory systems:
- Standalone barcode systems. These are simple software and scanner solutions that allow businesses to scan and track inventory with limited functionality without needing complex integrations. These systems typically use barcode scanners connected to a computer or mobile device to update basic inventory records or spreadsheets.
- Inventory management systems with integrated barcode functionality. Good inventory management software (IMS) includes built-in barcoding functionality. Unlike standalone barcode systems, which operate independently, these systems integrate barcode technology comprehensively with the larger production or distribution operation. This means large parts of inventory tracking are automated and data from barcode scans flows automatically between purchasing, production, order fulfillment, and other departments.
While both systems help improve accuracy, reduce errors, and make inventory management easier, integrated systems offer far more automation and efficiency gains.
How do you set up a barcode inventory system?
Setting up an integrated barcode inventory system is simpler than it seems when approached step-by-step. Here are some guidelines to help you get started:
Identify your business needs
First, assess your inventory management requirements. For example, if you produce electronics, you may need to track small, high-value components individually. As a food manufacturer, you may prioritize traceability for perishable raw materials and batch control. Defining these needs will help you choose the best inventory management solutions for improving inventory control and regulatory compliance.
Choose your barcode system
Decide whether to implement a basic barcode system as a standalone inventory tracking solution or to use advanced barcode inventory software. If opting for advanced software, make sure it supports the type of integrations with other production functionalities you’re planning to use. Also, check if the software allows for scanners or mobile devices to streamline inventory tracking.
Select your equipment
Also, pay attention to what type of hardware to use for the barcode system and its compatibility with your preferred software. Depending on your budget and the scale of your operations, choose between handheld laser scanners or smart device scanning apps. Also, secure a reliable printer capable of producing durable barcode labels that can withstand your storage or handling conditions. For example, a pharmaceutical manufacturer might need thermal transfer printers for long-lasting labels that can handle cold storage.
Integrating barcodes and production software
Integrating barcodes with manufacturing software enhances both accuracy and efficiency across operations. With systems like MRPeasy, barcodes become more than just labels—they’re tools for instant data access, tracking, and streamlined workflows. By assigning barcodes to inventory items, stock locations, and manufacturing orders, manufacturers reduce manual input, save time, and improve precision in every process step.
MRPeasy‘s barcode integration allows critical tasks like receiving goods, picking orders, and adjusting stock, to be executed with a quick scan. These automated updates ensure that inventory data remains current, enabling production planners and managers to make well-informed decisions based on real-time information. Barcode data flows seamlessly across tasks, keeping production processes synchronized and reducing the time spent verifying stock or locating items on the floor.
Costly barcode scanners are also no longer necessary. MRPeasy’s mobile app lets you turn any smartphone or tablet into a barcode scanner, allowing you to manage inventory from anywhere on the shop floor. This integration allows businesses to cut hardware costs and adds agility to inventory handling, making the entire operation more responsive and efficient. By linking barcode scanning with robust manufacturing software, your business builds a foundation for smarter, faster production management.
Key takeaways
- Barcode inventory control enables efficient and accurate stock tracking by reducing manual input, updating stock levels in real-time, and enhancing production workflows.
- Barcodes are valuable tools in inventory management, simplifying stock identification, streamlining receiving and shipping processes, and facilitating quicker physical counting.
- Inventory control is important for maintaining optimal stock levels to prevent production delays, reduce storage costs, and keep operations running smoothly.
- Setting up a barcode inventory system is straightforward when approached step-by-step. It involves carefully selecting inventory software, equipment, and integrations based on your specific business needs.
- Advanced inventory software includes built-in barcode functionality, automating data flow across departments, integrating with production tasks, and allowing smartphone scanning for flexible, cost-effective stock management.
Frequently asked questions
Inventory is managed by assigning a unique barcode to each item, which is then scanned at key points—like receiving, picking, and shipping. Each scan updates stock levels automatically in your inventory management system, reducing manual entry and improving accuracy.
A barcode inventory system is a tool that uses barcodes and scanners to track inventory items in real-time. This system updates stock data with each scan, simplifying processes like stock checks, order fulfillment, and item location.
Not necessarily. Many inventory management systems offer mobile app functionality, allowing you to use a smartphone or tablet as a barcode scanner, which helps reduce costs and increase flexibility compared to traditional barcode scanners.
Choosing the right barcode depends on your data needs and environment. For simple tracking, 1D barcodes work well. If you need to store more complex information, like batch or production details, consider 2D codes like QR or data matrix codes, especially if items also need to withstand harsher conditions.
You might also like: Why It’s Good to Have a B2B Customer Portal in Your ERP System