American Manufacturing – Past, Present, and Future
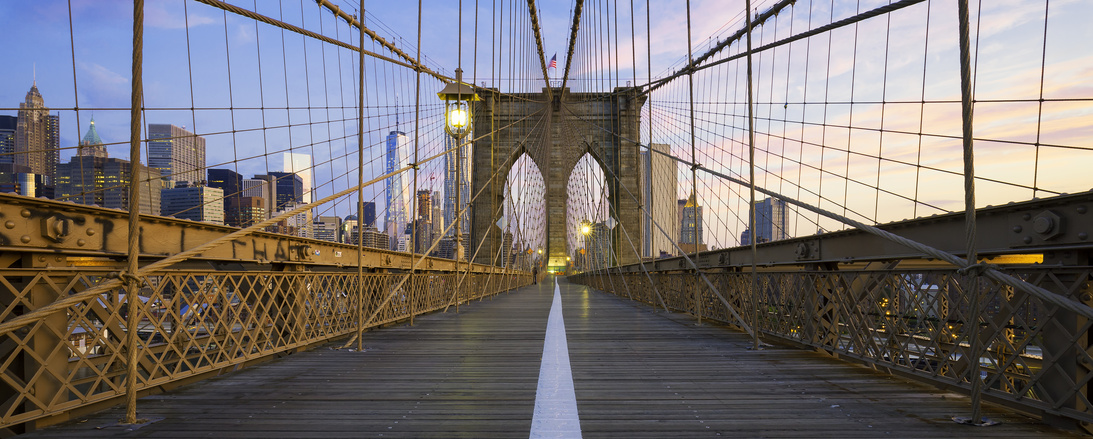
American manufacturing has undergone many changes over the years. Since mass production became possible, one thing has been certain – the future of manufacturing at any given time is uncertain.
But, there are things we can learn from the past that will help us to understand the present and make some assumptions about the future. This article will take a brief look at the history of American manufacturing, how it has progressed and developed over the years, the current picture and where things are likely to be heading in the not-too-distant future.
A brief history of American manufacturing
We have to go right back to the end of the 18th century to find the first seed of the American manufacturing revolution. In 1785, Oliver Evans pioneered an automated flour mill, using belt bucket pulleys, conveyors, and other ingenious devices to make his life easier. His ideas quickly caught on, and other flour producers began to automate their mills.
In 1790, Samuel Slater brought over to America some of the textile manufacturing techniques he had seen in England, building a water-powered cotton spinning mill. This directly led to a huge increase in the number of textile manufacturing companies, kickstarting the American industrial revolution.
The 1800’s saw industrial innovation in both Britain and the USA, such as steam and coal power and the birth of heavy industrial machinery. By the 1820’s factories were using steam-powered machines to begin the early stages of mass production. In the 1830’s locomotives had been invented and were revolutionizing industrial distribution.
The mid to late 19th century saw the development of the American System of Manufacturing, which utilized interchangeable parts and mechanized production. It became the standard that most American manufacturing companies adopted, and it led to the USA becoming a manufacturing powerhouse.
The 20th century saw a rapid change. From 1908, when the first Ford Model T came off the assembly line, to the 1970s and ’80s when robotics began to appear in factories, the growth of the United States manufacturing industry led to increasing globalization and innovation.
By the turn of the 21st century, the digital revolution had started, with computers, CAD software and advanced robotics transforming the manufacturing process.
Which brings us up to the present day and the dawn of an exciting new era in manufacturing.
The 4th Industrial Revolution – Industry 4.0
Industry 4.0 is a broad phenomenon that encompasses the revolutionary changes that are occurring in both domestic and industrial settings. It covers advancements such as the Internet of Things (IoT), Artificial Intelligence (AI), advanced robotics and Virtual or Augmented Reality (VR and AR).
In terms of the American manufacturing industry, we are starting to see these disruptive technologies being used more frequently across the board, from large international giants to small localized manufacturing companies.
The results of these changes are an upturn in productivity, cost savings, and increased competitiveness.
Processes such as additive manufacturing, also known as 3D printing, are taking things in a new direction. Prototypes can be made almost instantly, cutting down the product development cycle. Small production runs of customized products can be 3D printed, meaning that the cost of specialist parts and items will be reduced.
Another dramatic change in recent years has been the way that data is handled and communicated in the manufacturing environment. No longer do we have to rely on pen and paper to record output and process monitoring. Using a combination of IoT sensors and AI, computers can record relevant data such as inventory and production speed. Computer software can be used that brings all the data together, as well as making planning and scheduling tasks far easier. This is often known as Manufacturing Resource Planning (MRP) software. MRP software makes it possible for managers to oversee all manufacturing processes from one central place, meaning the decision-making process is more streamlined.
Companies are increasingly using cloud computing technologies to make full-automation of processes and data gathering a reality. Cloud computing offer advantages such as efficient transfer of data, centralized storage, and higher processing capabilities. When cloud computing is combined with well-developed AI systems and machine learning, valuable insights into manufacturing processes can be delivered straight to the dashboard of management staff who can act on them immediately. This is the power of Industry 4.0 and MRP software – monitoring, diagnosis and possible solutions can all be automated which will have a huge positive impact on productivity.
Today’s manufacturing challenges
As with all disruptive technologies, there are inevitable challenges.
Data integrity
The results of increasing automation and AI are all relative to the reliability of the data. If sensors or software isn’t installed or calibrated properly, then decisions are going to be made based on faulty data. One way around this is to improve the consistency of data collection and retrieval and to have a regular inspection programme to highlight problems within the monitoring system. Some automation and MRP systems have self-diagnosis built-in to test for integrity within the internal workings of the system for example.
Slow adoption
As with any new technology or revolutionary systems, there is likely to be a relatively slow adoption period. This is due to a combination of factors.
Firstly, the cost of installing new systems can seem prohibitive, but the high initial outlay is often recouped quickly with efficiency savings.
Another factor could be complacency, i.e. ‘We’ve always done it this way, and it has worked for years.’ This is especially true in the more traditional manufacturing environments, such as metalworking or making materials for construction. This attitude will hold back those companies, whereas companies that embrace change are more likely to prosper.
Job displacement
Just like the ‘Luddite’ textile workers of the early industrial revolution who were displaced due to increasing automation, today’s manufacturing workforce feel more and more threatened by automation.
But, there is hope for manufacturing employees. If they learn a new skill-set, there are plenty of new jobs available operating the computers that run the assembly lines and the MRP software that oversees everything. Yes, the overall number of employees is likely to be reduced, but for the most motivated, those willing to learn new skills, there will always be opportunities.
The SME manufacturing perspective
The challenges mentioned above are magnified for small to medium-sized manufacturing companies. The cost and disruption of overhauling existing processes and systems is off-putting. However, as Industry 4.0 marches on and new companies pop-up that are using the new technologies from the get-go, established businesses must stay competitive.
In other words, the best thing small manufacturing business owners can do is bite the bullet and jump on board the 4th industrial revolution. This doesn’t mean that they must install every new piece of technology that comes along, but there will be some essential systems, such as MRP software, that will give them that competitive edge.
U.S. manufacturing trends and what the future may hold
As stated at the beginning of this article, there’s always uncertainty about what the future may hold. Unfortunately, nobody has a crystal ball, so the best we can do is analyze the current trends and attempt to predict where things are heading.
The picture at the moment is increasing automation, data and AI-driven decision-making, additive manufacturing and the use of VR/AR.
If these trends continue, it’s likely that communication and management systems will become even more joined up. AI is likely to become more sophisticated, and it may come to the point where the entire manufacturing process from start to finish is 100% automated, with humans only stepping in to correct it when things go wrong. We’re probably quite a way off from this utopian (or dystopian, depending on your perspective) future.
Nobody really knows the effect that all of this will have on the overall industry. Forrester Research has stated that over 15 million new jobs will be created in the manufacturing sector over the next decade, but other reports say that 25 million jobs will be lost due to automation and AI.
One thing is for sure. The future of American manufacturing is likely to be characterized by intelligent data, communication and management, with companies that embrace AI, IoT technology and MRP software leading the way.