How to Track Actual Costs as a Growing Food Manufacturer?
Keeping track of your actual costs is vital for ensuring profitability, especially in industries like food where ingredient prices can be volatile. Here is how to track your actual production costs.
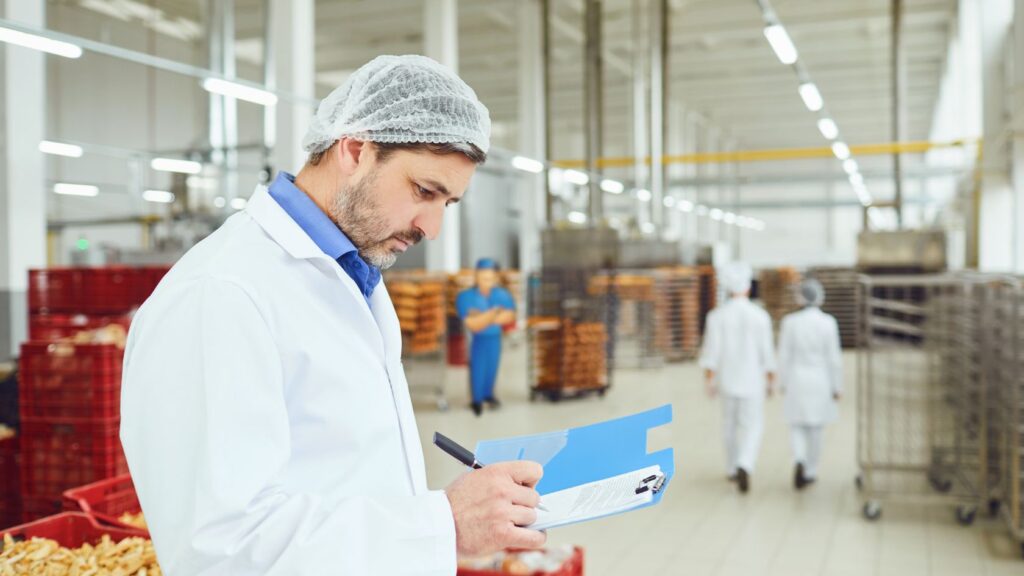
You can also listen to this article:
Why are actual costs important?
As a food manufacturer, understanding your actual costs is critical for pricing your products, finding financial sinkholes, and ensuring profitability. As opposed to the standard costs that are forecasted ahead of time, actual costs are the real costs incurred during production. These are recorded after the fact and can vary from the estimated standard costs due to ingredient price fluctuations, production run time variations, or changes in overhead costs such as utilities. Comparing the two enables you to get insights into your manufacturing operation’s cost-efficiency and start taking steps to better profitability.
Using spreadsheets for actual costing
Actual costing in spreadsheets involves meticulously tracking every expense related to the production of goods, including the costs of materials, labor, and overhead, and tying these to specific products, batches, and orders. This process can be highly complex and is made even more complicated as variable expenses fluctuate and your product portfolio grows.
The process starts by setting up structured spreadsheets that capture all relevant cost factors for each product batch. Calculating labor and overhead costs for a batch, based on the hours put into the production run, can be quite straightforward. However, the most complicated aspect of actual costing is associating each product batch with specific ingredient lots and their respective prices.
To effectively manage this complexity, each ingredient lot used in a product batch must be consistently recorded with precise details about the quantity used, the price paid per unit, and the supplier. This detail is crucial because price fluctuations in raw materials can significantly affect the overall cost of production. For example, if a batch of bread uses flour from two different lots purchased at different times at different prices, the cost calculation must accurately reflect the proportion of flour used from each lot to determine the true cost of the bread.
Moreover, this level of detail in tracking is not just about financial accuracy. It also supports operational decisions such as determining the most cost-effective ingredient lots to use, identifying potential cost savings by switching suppliers, or updating your prices to retain profitability. Furthermore, in cases of quality issues or supplier recalls, knowing exactly which products were made with specific ingredient lots can be critical for effective response strategies, including targeted product recalls.
However, maintaining such detailed records in a spreadsheet becomes unwieldy and error-prone as the volume of data grows. Spreadsheets lack the dynamic capabilities required for real-time updates and integration between departments, leading to an ever-increasing administrative load and siloed databases. Much of the data entry needed to keep spreadsheets up-to-date has to be done manually, making errors not a matter of “if” but “how many”.
Ultimately, while spreadsheets can be a starting point for small-scale operations, growing food manufacturers soon require more sophisticated solutions.
Using manufacturing software for actual costing
Food manufacturers need to keep an eye on hundreds of moving parts at once. Tracking dozens of ingredients coming in from various suppliers with varying prices, recording which ingredient lots were used in specific product lots, and gathering shop floor reports to check production run times and compile them into insightful statistics – it’s already enough to make your head spin.
That is why growing food manufacturers need specialized software that would enable full traceability and integrate all critical aspects of their operation. Here, manufacturing resource planning or MRP software stands out from other types of solutions such as those specializing in accounting or inventory management. Unlike other types of business management systems, MRP is a solution that caters specifically to the needs of manufacturers. This includes detailed manufacturing cost tracking capabilities often missing from other systems.
Following the journey of a product from ingredient suppliers through production to the customer, modern MRP software helps you record each direct and indirect cost, material handling transaction, inspection, and various other events, helping you achieve full traceability as well as transparency in your costs. The software automates much of the data entry necessary for maintaining meticulous records and provides you with an array of useful reports that help you make impactful business decisions. Moreover, integrating MRP software with your accounting software automates the exchange of information between the two, making record reconciliation a breeze.
In addition, food manufacturers can use MRP software to:
- Manage and develop product recipes (BOMs or bills of materials)
- Get complete visibility into their inventory
- Quickly forecast material requirements
- Accurately estimate costs and production lead times
- Automatically schedule and re-schedule production
- Track expiry dates to prevent spoilage
- Track quality inspections, identify the root causes of issues, and organize callbacks.
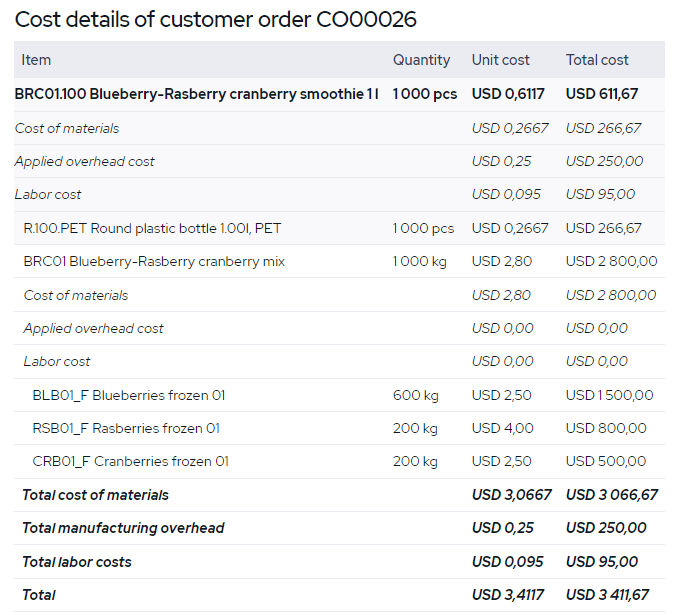
A real solution for real food manufacturers
For Frozen Garden, a frozen food manufacturer from Indiana, unreliable cost data became a major factor in the decision to find a better system that would allow them to automatically recalculate actual costs as ingredient prices changed and to perform detailed cost analysis.
“The old system could only give us cost estimates, not calculate actual costs,” says the founder of the company, Allyson Straka. “It couldn’t handle ingredient price changes, which started happening almost weekly.”
Luckily for Straka, she found a system that provided her with everything her company needed: cost control, FDA-compliant traceability, and production efficiency tracking.
“MRPeasy has all the functionality manufacturers from industries such as food or pharma need to comply with FDA regulations and get to the next level of efficiency,” she states.
Read the full case study: Frozen Food Manufacturer Raises Efficiency by 400%
Similarly, Pennsylvania-based food and beverage manufacturer Tait Farm Foods implemented MRPeasy to achieve traceability and get control over their inventory and costs.
“Before MRPeasy, I used to spend hours and hours trying to figure out the performance of our products and their costs and documenting them in Excel sheets,” says Nikki Mattern-Klinger, Production Manager. “The new system saves me so much time in doing this.”
With the new software keeping track of everything continuously, Tait Farm Foods has a much better grasp of its costs, which enables the team to quickly react whenever there’s a change in ingredient prices or labor costs.
“We are more profitable now because we know exactly what it costs us to make our products,” says Sales Manager, Karen Addenbrook. “And we can increase or decrease our prices as we go along.”
Read the full case study: Specialty Food Manufacturer Meets FDA Requirements and Sustains Growth
Key takeaways
- Actual costs provide a clear and accurate picture of what it really costs to make your products, which is essential for pricing correctly, identifying financial inefficiencies, and maintaining profitability. They account for real-time fluctuations in costs due to ingredient price changes, production run time variations, or changes in overhead costs.
- Small operations often begin by using spreadsheets to track costs, reconciling financial data manually between spreadsheets and accounting software.
- Growing businesses should consider shifting from basic tools to more robust manufacturing resource planning (MRP) software. This software can handle complex tracking needs such as multiple ingredient sources, price changes, and production run times, and provides comprehensive reports and analysis capabilities.
- Utilize an MRP system to automate data entry, track all production costs, manage inventory, and analyze product profitability. This not only saves time but also improves accuracy and provides insights that can drive business decisions and improve operational efficiency.
- For industries like food manufacturing where compliance and traceability are crucial, MRP software ensures you meet regulatory standards while giving you complete control over your production costs and processes.