Actual Costing Guide for Manufacturers
Actual costing, or keeping track of your actual costs, is vital for ensuring profitability, especially in industries where production costs fluctuate. Here is how and why to implement actual costing in your company.
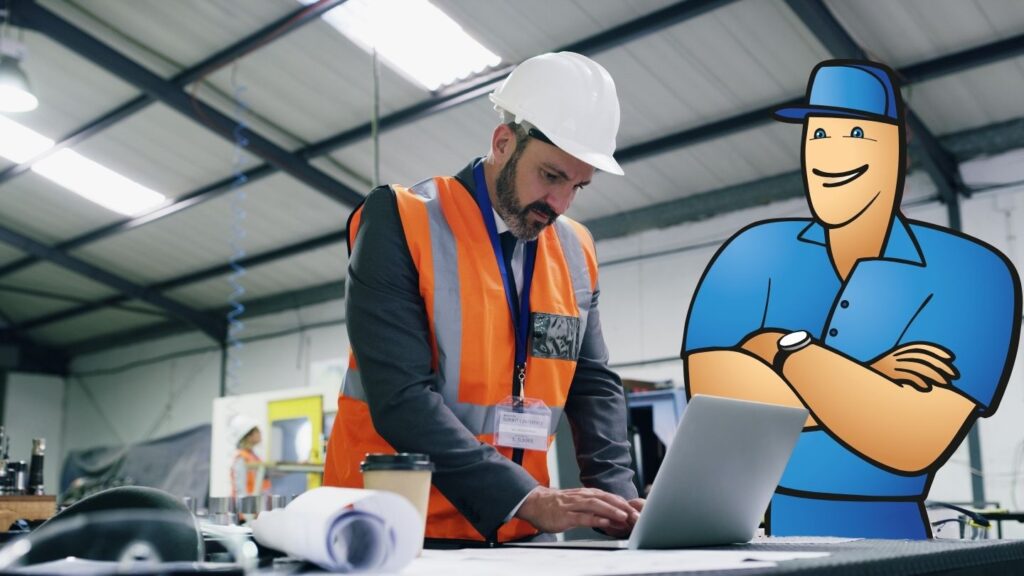
What is actual costing?
Actual costing is a specific cost accounting method that precisely records real costs incurred during production, including direct material, direct labor, and manufacturing overhead costs. Unlike standard costing, which relies on estimated costs, actual costing tracks expenses as they happen, enabling manufacturers to understand the true cost of their products or orders. This approach is invaluable for businesses with volatile material, labor, or overhead costs where cost estimating can be highly inaccurate.
To address any confusion, we would like to note that in this article, we are discussing the “actual costing” method of determining the cost of a manufactured product. While in non-accounting environments, in everyday language, the similar term ‘actual cost’ may often be used to describe something related but distinct. For example, when someone says that “the actual cost of X is…”, they may refer to the cost of goods in your books (regardless of the method of how it is determined) in contrast to the estimated cost, which refers to the (past or future) expected cost of the same item.
Actual costing vs. normal costing vs. standard costing
Each costing method—actual costing, normal costing, and standard costing—offers unique approaches to calculating production costs and is suited to different types of manufacturing operations:
Actual costing
Actual costing tracks real costs for materials, labor, and manufacturing overhead incurred during production. This method provides precise cost data but can be complex and time-consuming due to the need for meticulous record-keeping. It is best for manufacturers who need detailed cost accuracy, especially when dealing with fluctuating material, labor, or overhead expenses. However, the real ‘actual costs’ can only be calculated when overhead expenses are combined at the end of the accounting period; therefore, normal costing is used for real-time cost tracking.
Normal costing
Normal costing is a subset of actual costing that combines actual costs for direct materials and labor with a predetermined overhead rate to calculate total costs. It strikes a balance between the accuracy of actual costing and the simplicity of standard costing, enabling real-time cost insights without requiring exhaustive data tracking. This approach is ideal for manufacturers that need to get continuous updates regarding their production costs or in situations with consistent overhead costs.
Standard costing
Standard costing relies on predetermined costs based on historical data or expected averages for materials, labor, and overhead. While easy to implement, it does not reflect real-time costs, making it inaccurate for businesses in dynamic environments. This method works well for manufacturers with stable processes and predictable costs.
Benefits of actual and normal costing
Understanding how much money you spend on manufacturing your products is critical for maintaining and growing profitability. Here is how actual and normal costing can benefit your business:
Understanding where your money goes
With actual and normal costing, manufacturers can understand where money is spent across different cost objects, like specific units, batches, or customer orders. This helps track actual material and labor costs associated with each cost object, providing clarity on how resources are allocated throughout the production process. By identifying cost patterns across various cost objects, manufacturers can pinpoint specific areas where they could improve efficiency or reduce expenses.
Deciding how much your products should cost
Normal costing enables manufacturers to calculate the total cost associated with each cost object, factoring in actual direct costs. This real-time information helps set prices that cover the production costs for each cost object, ensuring profitability without relying on budget estimates. If the costs are higher than expected, manufacturers can understand which components (e.g., variable labor costs or material expenses) are driving the increases.
Reacting quickly to cost fluctuations
Normal costing enables manufacturers to respond rapidly to cost fluctuations. When material costs or labor rates increase, a normal costing system provides immediate insights into how these shifts impact unit or order costs. For instance, if the cost of a material rises, manufacturers can quickly switch suppliers or adjust the product’s bill of materials or selling price.
Budgeting and forecasting
Using actual or normal costing makes budgeting and forecasting more accurate by basing predictions on real historical data. Rather than relying solely on standard costs, manufacturers can project future costs based on actual expenses recorded in previous accounting periods, allowing for more accurate budgeting. For instance, if actual data indicates a steady rise in labor costs associated with certain products, manufacturers can adjust budgets to reflect this trend.
Increasing profitability
Actual and normal costing provide visibility into the true costs associated with each product or order, enabling manufacturers to identify and control inefficiencies, such as excess labor hours or material waste. By tracking the exact costs for each order or unit, manufacturers can make data-driven adjustments to reduce expenses. Additionally, actual costing enables manufacturers to set prices that reflect the real expenses involved in production, ensuring that each product covers its costs. When actual costs reveal unexpected increases, manufacturers can adjust prices to protect profit margins and ensure sustainable growth even as market conditions or material prices fluctuate.
Tracking actual costs in spreadsheets
Using spreadsheets for actual costing entails meticulously tracking material, labor, and overhead costs and tying them to specific products, batches, and orders. While theoretically possible, this process is highly complex and requires constant attention.
To begin, structured spreadsheets must be created to capture all relevant cost components for each product batch. Labor and overhead costs can be calculated relatively simply by recording the hours worked for a production run. However, the real challenge lies in associating each product batch with the correct material lots and their respective costs.
This requires recording detailed information for each material lot, including quantities used, unit prices, and suppliers. This detail is critical, as raw material price fluctuations can significantly impact production costs. For instance, if a batch of bread is made with flour from two different lots with varying purchase prices, the spreadsheet must accurately reflect the proportional use of each lot to determine the batch’s true cost.
This level of detail not only ensures financial accuracy but also supports operational decisions, such as identifying cost-saving opportunities or selecting more cost-effective material lots. Additionally, in cases of recalls or quality issues, precise tracking allows manufacturers to trace affected products and do targeted callbacks.
However, as data volume increases, managing all of this in spreadsheets becomes time-consuming and error-prone. Spreadsheets lack real-time updates or integration with other systems, such as inventory and procurement—capabilities that are essential for modern manufacturing. While spreadsheets may be enough for small-scale operations, more complex businesses typically require specialized software solutions to handle the intricate demands of actual costing.
Tracking actual costs with manufacturing ERP
Small manufacturers often rely on spreadsheets and accounting software to track costs in their early stages. While this approach may work initially, it quickly becomes overwhelming as production grows. Managing materials from multiple suppliers with fluctuating prices, linking material lots to specific products or production batches, and collecting shop floor data for insights can be too complex for manual systems.
Manufacturing ERP software such as MRPeasy provides a better solution by streamlining normal and actual costing and ensuring full traceability of costs across the production process. Unlike generic accounting or inventory systems, MRPeasy is designed to track material and labor costs in real time and tie them to specific stock lots, orders, and products. This allows you to continuously monitor your manufacturing costs, flag cost variances, and take action, e.g. by adjusting selling prices or choosing more affordable suppliers.
In addition, by tying BOMs and production routings to material and labor costs, manufacturing ERP enables you to accurately estimate production costs when quoting. Integration with accounting software further simplifies workflows by automating the exchange of cost data, making record reconciliation seamless.
Key takeaways
- Actual costing records real expenses for materials, labor, and overhead during production, providing precise cost data for manufacturers.
- Actual costing offers high accuracy but is time-intensive, while normal costing balances real-time insights with efficiency by using actual material and labor costs alongside predetermined overhead rates. Standard costing is easier to implement but less precise, as it relies on estimated averages.
- Actual and normal costing enable manufacturers to track where money is spent, set accurate product prices, and respond swiftly to cost fluctuations.
- While spreadsheets can be a starting point for tracking actual costs, they become inefficient and error-prone as production scales.
- Manufacturing ERP systems streamline normal and actual costing by providing real-time cost tracking, tying costs to specific orders or stock lots, and automating data management. This enables manufacturers to monitor costs continuously, identify variances, and make strategic adjustments.
Frequently asked questions (FAQ)
The choice depends on your production complexity and need for accuracy. If your costs fluctuate frequently, actual costing is ideal for precision. For real-time tracking without exhaustive record-keeping, normal costing is a good middle ground. Standard costing works best for stable production processes with predictable costs.
While theoretically possible, implementing actual costing without ERP software is challenging and prone to errors, especially as production scales. Manual methods like spreadsheets require meticulous data tracking and are not efficient for handling real-time updates or cost variances, making ERP software a better option for accuracy and scalability.
Actual costing directly impacts profitability by providing precise insights into true production costs. This enables manufacturers to set accurate prices, identify inefficiencies, and make data-driven decisions, ensuring that every product sold covers its costs and contributes to the bottom line.
You may also like: Periodic vs. Perpetual Inventory System