3 Real-Life Electronics Manufacturing Challenges Resolved with MRP Software
Managing the manufacture of electronics could be as complicated as the products themselves are. This complexity can be significantly reduced with powerful software now accessible to manufacturers of any size. Here are three real-life examples of issues electronics manufacturers face and how MRP software can help resolve them.
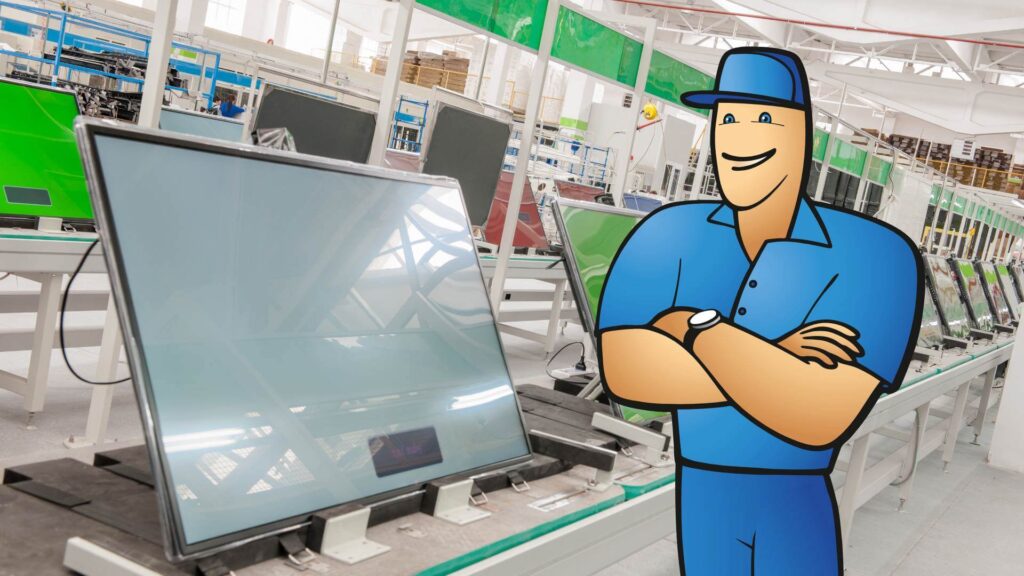
You can also listen to this article:
Managing complex bills of materials
Efficient management of BOMs is crucial for precise production planning and scheduling. Understanding the components of a BOM and their interdependencies ensures resources are correctly allocated, necessary parts are available on time, and the production flow is smooth. In essence, well-documented and -managed BOMs provide a clear roadmap for production, enabling an accurate and efficient production schedule.
Moreover, with the effective management of multi-level and configurable BOMs, manufacturers can handle variations of intricate products, manage diverse product lines, and adapt to customer-specific requirements without disrupting or needlessly complicating the overall production process.
One of the biggest challenges in electronics BOM management is keeping track of product changes and updates, which is where version and revision control comes into play. By implementing a system that tracks each change in a product’s bill of materials, manufacturers can make sure that production is always based on the latest BOM version, thereby preventing costly mistakes and confusion. Version control also allows product engineers to easily revert back to previous versions of the BOM.
Managing configurable, constantly changing BOMs with tens or hundreds of subassemblies in spreadsheets is close to impossible. However, by implementing cloud-based MRP software, electronics manufacturers can simplify BOM management, ensuring accurate production planning and scheduling. Moreover, with robust version control features, it safeguards against costly mistakes and confusion by tracking product changes in real time and enabling seamless transitions between BOM versions.
“When we start producing new items, drawing up new bills of materials and getting them linked up with production planning takes just a few hours now instead of days,” says Kendra Scappaticci, Operations Manager at KS2, a Canadian automotive battery and electronics manufacturer. “Thanks to MRPeasy, we can upload a new BOM, be ready to submit manufacturing orders, and send out invoices associated with the new product within the same day now.”
Communication gaps between departments and facilities
In an electronics manufacturing setup, synergy between different departments is crucial for overall productivity. Traditional siloed systems wherein each department uses separate software or documents often lead to communication gaps, resulting in errors and bottlenecks. Cloud-based MRP software facilitates the seamless integration of all departments, facilities, and even subcontractors into a single system.
This software allows the real-time sharing of information, making pertinent data instantly available for all the parties involved. For instance, a change in the BOM by the engineering department or an approved customer order can be instantly visible to procurement, inventory, and production teams. This helps in faster decision-making and effective resource management.
Another perk of cloud-based software is that it accommodates scalability and geographical diversification effortlessly. Whether a company operates from multiple production or warehousing sites or even manages remote work scenarios, the software ensures that communication and data access are never compromised as long as an internet connection is available.
“We had staff in two locations in the US, plus the procurement department in Taiwan, therefore we needed a system that could be accessed from anywhere,” says Dennis Lan, Supply Chain Director at Anthem One, an LED lighting solutions manufacturer from Arizona. “Before implementing MRPeasy, it was hard to tell which part was where. Now, we know exactly.”
Traceability and regulatory compliance
Traceability in the supply chain is pivotal for electronics manufacturers for several reasons, ranging from compliance with regulatory standards to managing returns and recalls. With cloud-based MRP software, tracking every component, right from procurement through production to the final product shipment, is achievable.
Quality inspections can be tracked and recorded systematically. In case of a quality issue, the software aids in identifying the root causes by tracking back the specific batch, a particular component, or the employee involved. This swift identification and resolution of problems significantly reduce downtime and enhance customer satisfaction.
Moreover, the software’s Return Material Authorization (RMA) module can streamline returns and recall management. With it, tracking the return journey of a faulty product, analyzing the issue, executing corrective measures, and documenting these processes are seamless and efficient.
“With the software, I’m able to track components and achieve traceability throughout the order chain,” says Ralph Jones, Director at Britannia 2000 Holdings, an aerospace electronics manufacturer. “So, if we have a bad batch, we can find out which MOs and POs they were part of. Everything we manufacture is serial numbered and MRPeasy helps us track these as well.”
You may also like: 7 Real-Life Manufacturing Challenges Resolved with MRP Software