12 Tips for Successful ERP/MRP Implementation in a Manufacturing Company
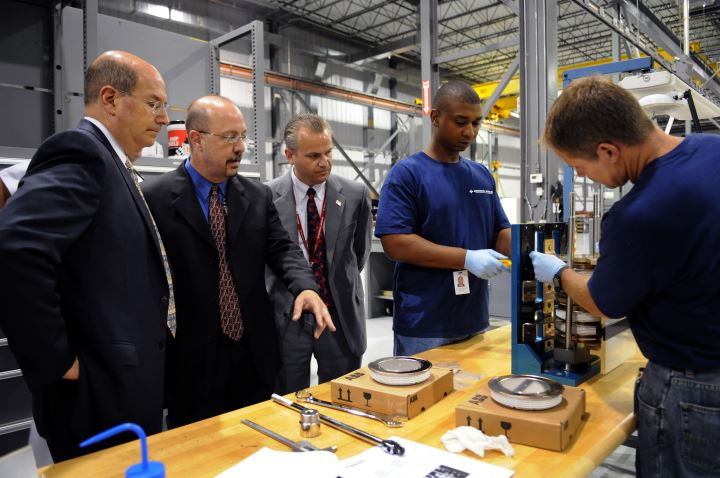
You can also listen to this article:
These tips could help you, if you have used ERP/MRP software previously, but you do not have your own experience in implementation of ERP/MRP systems.
1. Company Size Matters
Not every company is ready to implement an ERP/MRP system anytime. This is especially true for micro-companies (up to 10 employees). Such companies may not have enough resources and competence for the ERP/MRP system installation and operation. Also, the outcome of using manufacturing ERP software in such a company can be less than expected.
2. Avoid Micro-tasking
ERP/MRP system is intended to solve major problems associated with manufacturing, so try to identify important tasks, since they will have the most impact while focusing on micro-automation will lead to more complexity of the implementation project.
Set a limited number of major implementation project goals which should be closely related to the business processes and problems that you want to solve. Don’t waste time and energy on tasks which look nice, but have a small impact. Goals should relate to the business, rather than automation itself.
3. Allocate Enough Resources
The ERP/MRP system implementation process is a one-time, but quite a big project, so allocate resources accordingly. Set a project manager for the implementation process with enough time resources, as well as with experience in ERP/MRP software. All heads of departments that will use the system should be included in the implementation project team.
4. ERP Implementation Step by Step
Depending on your company’s size and structure, you can implement the system by module, by functionality and by personnel, for example, when in the beginning the managers report about finished manufacturing orders on their own before passing this function to line workers.
5. Data Classification
Think over data classification and categorization. Create logical product groups. It is near impossible to change data classification after installation.
6. Keep Testing and Implementation Apart
Have a clear understanding – are you testing, or implementing the ERP with real data already. Using real data during the testing period will make the process over-complicated. Cleaning the database if the data are mixed with test data might be problematic.
7. Customization is not the Only way
It is practically impossible to find an ERP solution that would suit all the needs and align perfectly with your existing business processes and documents. In most cases you have to adapt or customize. Though customization might seem as the simplest solution, on practice adapting your business processes could be more effective, and may deliver better results in the long-run.
8. Keep Future Users Informed About Goals and Project Schedule
Make sure that all the users that will be interacting with the ERP system have a clear understanding of implementation goals and schedule. This means that one general meeting in the beginning of implementation should be held with periodic communication to follow.
9. Users Must be Trained
Every person interacting with the ERP software should be aware of what one is doing. Usually the first one or two trained users pass the knowledge to others. Another option would be software vendor’s trainings.
10. Experience with ERP/MRP Systems Helps
The implementation project team leader should have prior experience with using and/or implementing ERP systems in your specific industry. If you don’t have such a person, then it is good to find a partner consulting company with such experience.
11. No Rush – Test and Test Again
Test intensively prior to start using an ERP system in production mode. It is much easier to fix errors during the testing period than during operating with real data.
12. Keep Old System Working
It is better to use the old system in parallel with the new one for at least 1-2 months after having implemented the new ERP software. This helps to make sure that the new solution has been configured and is being used properly, for example the reports in old and new systems are identical.
Also, in case of major issues with the new system you will be able to roll back to the old.
Hope this helps! Let us know if you have any questions.